After not posting a construction thread for way too long I'm jumping back in, but I'm venturing out into unfamiliar territory: O scale! I've watched Karl, Joel, and others construct amazing models with stunning details that I felt were beyond my reach in HO. Add the legendary CHB machinery along with my love of logging and the O scale sawmill kit was an obvious choice for my next project.
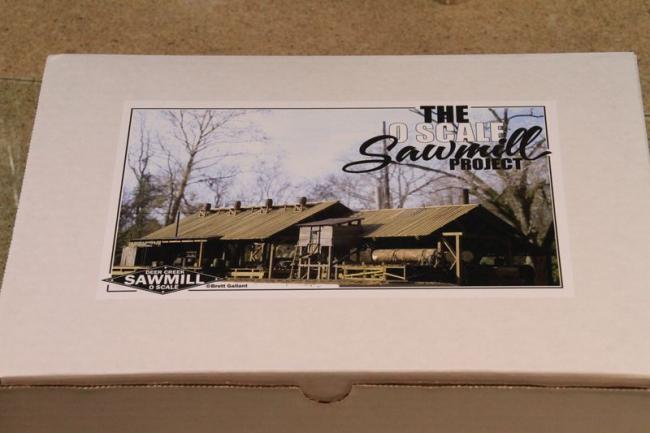
I actually began building it in March of last year. I've been researching sawmills, stockpiling pictures, and collecting larger scale techniques and ideas for even longer. I knew I wanted to include a water feature in the diorama and that would require some considerable changes to the original model. (One change has a habit of altering 4 or 5 elements down the line!) All that being said, I need to thank Brett right off the bat. He helped me work through numerous obstacles and hurdles that I created while trying to incorporate my ideas. Also Karl, Ken, Alan and Joel have shared their insights and second opinions when my self-doubt would get the best of me. You guys are some of the most talented modelers in the hobby and I can't thank you enough for chiming in when the call went out!
This won't be a typical step-by-step construction thread for a couple reasons...
1) The O scale mill has been well documented here on the forum
2) I lost a ton of pictures when my camera's memory card crashed. Bummer!
I'll try to stitch together the pictures and document the build as best as I can. I've been experimenting along the way and I'll be sharing some pretty cool and useful techniques that worked well for me. So, here we go.
Not that it stays this way for very long, but THIS is what my workshop looks like when it's clean:
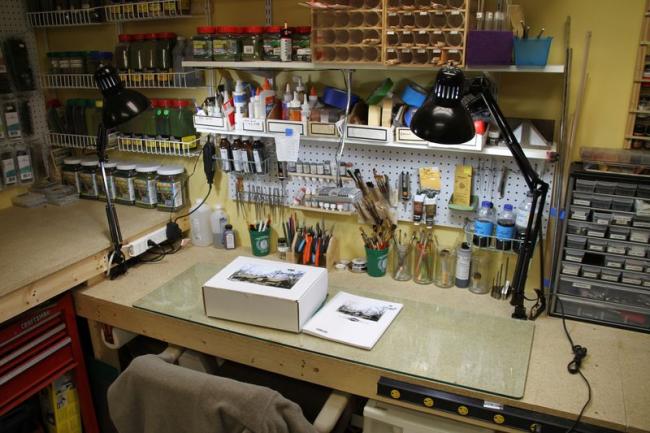
The footprint for my version is 4 feet x 2 1/2 feet. The log pond will be situated in the upper right in the next picture. The mill subfloor is complete at this stage and stands on a large collection of weathered piers. It's test fit on the diorama base along with an initial layer of dirt (sanded tile grout).
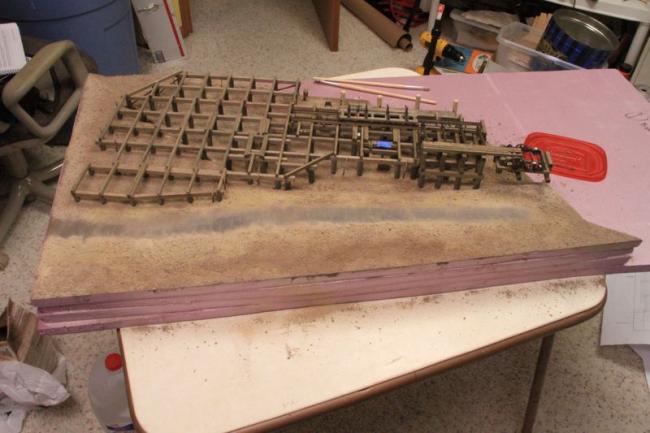
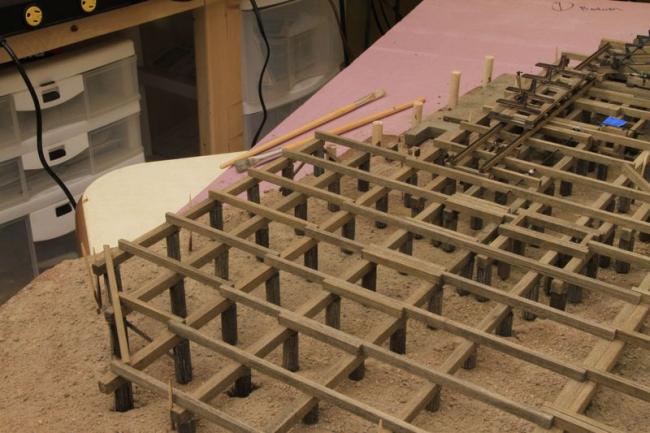
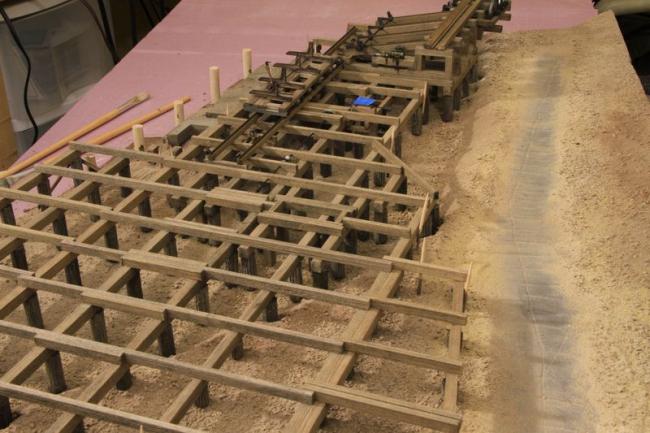
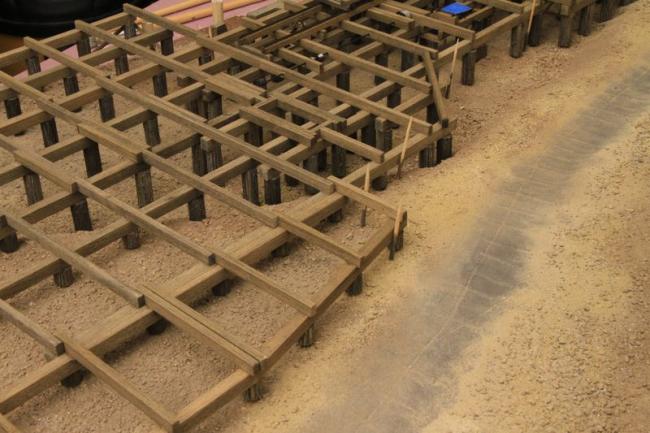
Next update, we'll take a look at the log haul machinery (which isn't part of the current kit #308).
Bill
Comments
Jerry
MikeM--as far as the lost pictures, I took the card straight to a local camera shop. I was using a ProMaster Compact Flash memory card (the kind that newspaper photographers use). My camera shop has some specialized software and tools to extract files that would otherwise be lost. No luck. Unfortunately, when a card like this is "guaranteed for life" and it fails...all that means is they give you a new card--not the missing pictures!
Such is life!
By including the log pond and log haul, I changed the mill's order of operations. As explained in the manual, the raw timber was brought by rail to the mill and unloaded onto the rollway skid. In my model, the logs are delivered up the green chain from the pond. So I changed a major function of the rail service: Rather than delivering fresh cut trees, the trains would now haul away the rough sawn boards (product lumber). That involved moving the rails to the opposite side of the mill. At this stage of construction, that was an easy change achieved with a Sharpie!
Here comes the real work...
One of the first orders of business was to adapt the Log Deck and log haul to fit the structure. These two features are not part of the O scale kit. They were a couple of items that, I believe, Brett acquired along with the rest of the CHB line. So, my version will look completely different than the original rollway (pictured on pge. 26-29 of the O scale manual):
Mine is at an angle and has 4 rails that the logs roll down. The supporting frame also needed to be condensed and allow for correct alignment with the log carriage, carriage drive, and structural elements of the mill itself. After bouncing some ideas off Brett, here's the configuration that resulted:
In looking at the last photo, the supports have kind of a "hodge podge" appearance (that's because...well, it WAS!). However, the majority of the framework that supports the skidway will be hidden by a walkway that will give the workers a way to get from place to place . Also, you can see that there's nothing supporting the log haul machinery. That gets added later (after I determined the height of the log haul, the depth of the log pond, and changes that needed to be made to the shoreline).
The log haul machinery is unbelievable! (In fact, the same can be said for ALL the castings and machines in the kit). The level of detail is stunning and I wanted to take full advantage of all of it. I mentioned in my Deer Creek mine build that I was experimenting with mineral spirits and chalk (rather than alcohol and chalk) on some of the metal castings. The mineral spirits can give a softer transition from weathered vs. unweathered areas. I went that route again on the log haul: the sections of the spokes show more rust near the hub as opposed to the areas toward the wheel. It seemed to me that there's a lot of metal-on-metal contact in that area, plus it gives the gears a little contrast and definition.
After that, I added grease build-up and oil stains using dark chalk (raw umber 408.3 and some straight black in a couple spots) and MIG "Fresh Engine Oil." I'll go deeper into this process later in the build.
Here's how it looks connected to the sub-floor:
I realize that I'm bouncing around quite a bit and I'm documenting my progress using some lousy pictures. But hopefully, it'll make more sense as we progress. Any questions that I can answer... fire away!
I'm going to get deeper into the machinery construction in the next update.
Bill
Karl.A
Will be interesting on how you did the grease and oil stains.
Jerry
Much appreciated and glad to have you along. Your original build provided a lot of inspiration and answers as I went along.
Jerry-
Thanks for the kind words. I'll get into the oil & grease very shortly.
Bryan-
I referred to your model many times as well! Texturing the dowels can tear up more than a few wire brushes, for sure. To get some really deep grain and texture, I tore into them with a nail board. I clustered up a bunch of finishing nails leaving the points exposed and then give the dowels several back n forth passes:
Robert
MikeM--that's probably where I got the nail board idea. Pete Vassler does some amazing work!
The machinery in the O scale sawmill is as close to art as you can get. The accuracy and detail are stunning. The boiler and steam engine provide power to the husk saw, log carriage, live rolls and log turner, and also the cut off saw and edger. Assembly of all these items is nothing difficult. However, the parts are identified right off of the machinist's drawings. If you're not familiar with working from mechanical drawings (like me!) it's not a bad idea to label and organize all the components.
For example, on a two dimensional drawing, a front pressure roll and a rear pressure roll look pretty similar (parts 6 & 7). But when laid out and identified, there's a major difference between them:
I found that it was time well spent to count, separate, and identify by number EVERY part for each machine. Again, assembly was straight forward once I was familiar with what goes where.
I wanted to "dirty up" certain machines and components to give them an appearance of being in service for many years. This picture shows what I was going for: the accumulation of grease, oil and grime around the moving parts and different surfaces. Some places have what looks like fresh, leaking oil; other spots have a build-up of "gunk" and grease:
Using the log haul, here's a basic step-by-step of how I got my results. The "Oil & Fuel weathering set" from Ammo by Mig Jimenez has 3 different types of oil and grease stains and works great. You can get this set on amazon or a hobby shop:
I began by applying small splotches of "Engine Grime" (a grayish satin-sheen oil residue) to the areas around the pillow blocks:
While the engine grime is still wet, I added a really light layer of chalk (raw umber 408.3). By "light layer" I don't mean the amount of chalk, but the size of the particles. Rather than a blade to shave off some chalk dust, I used a small make-up brush to create a "cloud" of chalk powder (the idea is to get the chalk so fine that it almost looks like a puff of smoke):
I let this cloud of chalk build up so that it soaks up the wet paint. This first layer has a grayish color and a flat finish. You can (hopefully) see where the chalk has accumulated on top of the pillow blocks:
Next, I repeat the process but this time I use "Fuel Stains". This paint is a clear brownish-black and has a glossy finish when dry. I add tiny drops of the paint on top of the patches just created, on top of the pillow blocks, and around the line shafts where they stick out of the pillow blocks. I follow that with a "cloud" of chalk, let it settle onto and absorb the wet paint:
For the vertical oil drips, I used the same "Fuel Stains" applied with a really tiny brush. Rather than paint them in freestyle, I use a machinist's square and rest the brush against it. That way the drips will be perfectly straight up and down and parallel to the others:
Another application of "Fuel Stains" and chalk but this time a little lighter in color (408.5 and 408.7). The lighter chalk adds some definition and is a nice contrast to the previous layer--which will look almost black. The repeated applications help create the illusion of that fuzzy film of grease:
Once I got to a point where I liked the look, I let everything dry overnight and reevaluated the next day. For the most part, once completely dry, it looks a lot like the last picture above--sort of damp and grimy. Once it was 100% dry, I went back and added a few tiny drops of the Fuel Stains here and there so that there were some fresh oil spots.
The final step is to take and rub a #2 pencil over the teeth of the gears so that they shine a bright silver from the repeated metal on metal contact.
Here are a few shots from both sides of the haul mechanism. Terrible lighting on the first two, but here are a few close ups of the effect:
Keep up the fine art!
Mark
Do you mean on the sides of the gear and gear teeth? Like here:
Does that make sense?
Mark
Jerry
Mike-
I had talked to Brett about getting these included with the SW paints. The issue is that the SW paints are acrylic and the Mig stuff is enamel.
In my research, I learned a lot about these beasts:
*the blades were pretty massive (6-8 feet in diameter was not uncommon)
*they generated a lot of heat when cutting and were usually cooled with water
*when in use, they look reflective and shiny
On the other hand...this dude hasn't seen action in years:
I began by blackening all the metal components and polished up the ones that needed to look shiny (the surfaces of the drive wheels) with a felt buffing pad and this little Dremel polishing wheel:
The frame and supporting structure I left black and again added a layer of "shop gunk" just like on the log haul. This time, I used a couple shades of raw umber chalk along with a blackish-brown enamel wash (Mig "Track Wash") and the fuel stains paint (for the wet, oily areas).
Same process as before: dampen the piece with Track Wash; let a cloud of chalk snow down on the area and absorb the enamel paint. I repeat this process using less and less paint and more and more chalk until it's built up to a fuzzy layer.
Try as I might, I couldn't color and weather the paper saw blades to convey that ferocity described above. So, I went on the hunt for real metal blades and found these at Harbor Freight:
The lettering was removed by spinning the blades in my Dremel and scratching it off. I think I used everything from sandpaper to emory boards and files and even an old sharpening stone. That also helped scribe in wear marks and deep scratches:
Two issues with using these little hobby blades:
First, the holes in the center were too big for the blade hub on the model. So, using a paper punch and some heavy aluminum foil I punched out some circular filler pieces and added one to the hole in the blade. Then, I poked a hole in the center of the foil so that the blade arbor shaft could stick through. Attach the blade nut to the shaft and issue #1 was solved!
The second issue was the size of the hobby blades. Using the biggest one was out of the question. Way too big. Using two of the second biggest baldes was close:
...yet so far away:
So, I opted to model mine like the double blade saw pictured above: a large blade on the bottom and a smaller blade on top. Not perfect, but a plausible solution.
Here's the saw positioned in the mill:
I also wanted to model that greasy work area that you can kind of see in the double blade picture above (near the feet of the guy with the green shirt). I measured and cut some floor planks for the spot where the operator stands. I did my thing with Fresh Oil paint and 408.3 chalk but built it up only on the sides closest to the saw. That way, it would look like the water and oil pooled right at the base of the machine.
It takes repeated applications of straight up Fuel Stains paint in order for it to stay wet looking. It would keep getting soaked up by the chalk, I guess. But eventually, I got a couple wet looking oil spots on top of the "shop gunk". It's in an area that's tough to photograph, but here's a shot of it today:
Jerry